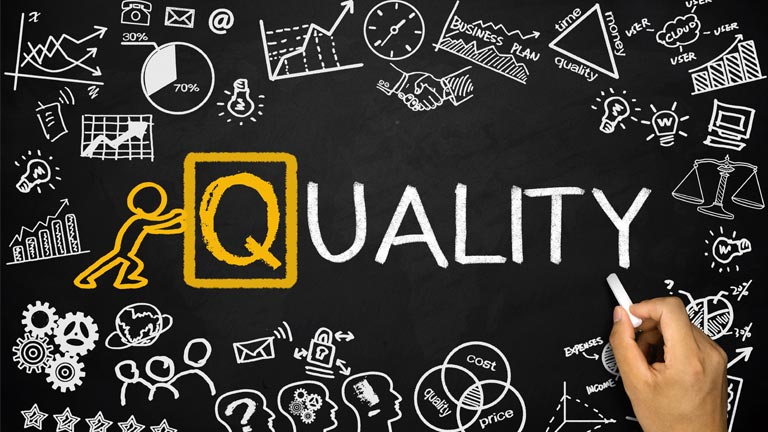
Daikin is the world leader in the air conditioning industry, serving customers in almost 145 countries. With over 80 production bases worldwide, it sells more than 7,000,000 units of air conditioners every year. Our quality products are used for commercial as well as residential purposes. The commitment towards offering only quality products is the result of centuries of experiment, in-depth knowledge and continuous research and development. Today, we have established regional R&D base all around the world such as China, U.S.A, Belgium, India, Japan, and Thailand, which realizes the unique needs of the particular region and works toward creating suitable products according to their climate and lifestyle.
Established in Osaka, Japan, in the year 1942, we are a 100-year old company, thriving to offer the best air conditioning systems. In the year 1951, we manufactured Japan’s first package type air conditioner. Similarly, in 1982, we launched Japan’s first commercial multi-split type air conditioner (VRV). We were also the first to launch ‘Ururu Sarara’, the world’s first residential air conditioner equipped with a humidifying unit. We also set the benchmark in 2012 by launching ‘Urusara 7’, the world’s first residential air conditioner to adopt the next generation refrigerant R32. Additionally, in 2015, we founded the Technology and Innovation Center in Osaka, Japan, to gather and collaborate information from various sources. We are also the one and only brand that develops and manufactures all the core components in an air conditioner such as a compressor, motor, and refrigerant.
We, at Daikin, firmly believe that design and development are the two most crucial components for making a high-quality product. We have a designated team of developers who work hard to create exceptional and sturdy designs for years of hassle-free operation. During the process of development, around 700 parts are immaculately designed and manufactured. These components are then individually tested to perform for best results. Also, we boast of a hi-tech facility at each R&D base, where only the best testing equipment is used. These high-tech testing equipment ensure that only the efficient and long lasting products are approved according to market standards. Before these designs are approved for production each prototype goes through 300 rigorous tests in 7 different categories.
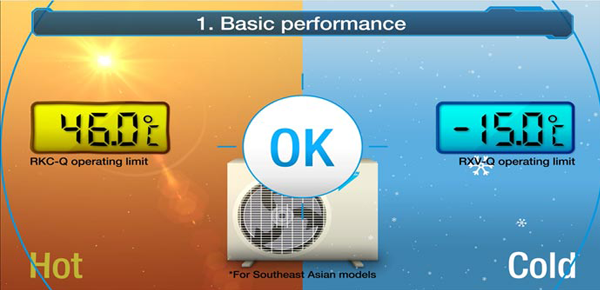
The first test i.e., the Basic Performance test, ensures that the AC performs efficiently even under extremely high or low temperatures.
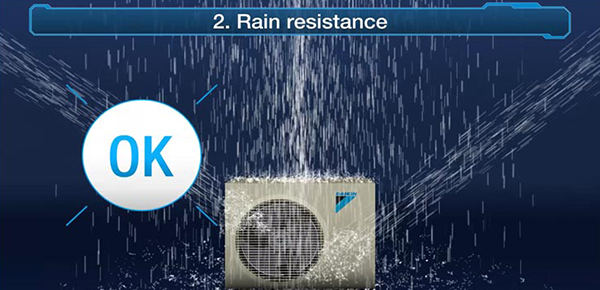
The second is the Rain Resistance test which ensures that the AC operates normally in high humidity or during heavy rainfall.
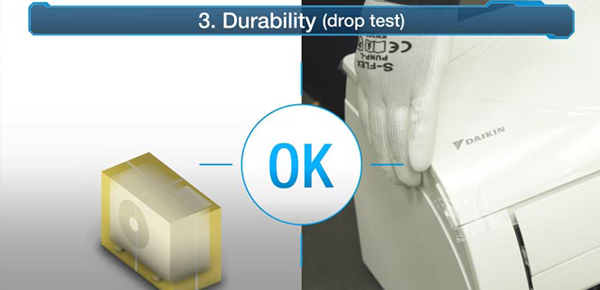
The third test is the Durability test which confirms that the AC operates normally even if it’s dropped during transport.
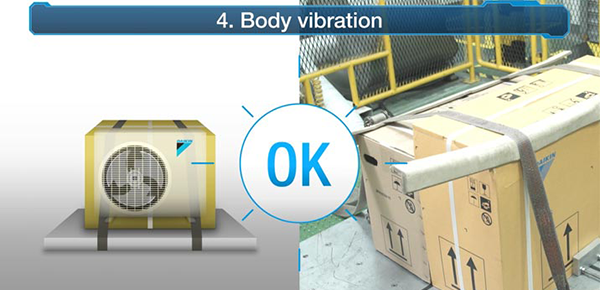
The fourth test is the Body Vibration test which ensures that the AC remains intact and functions normally even when it’s shipped long distances.

The fifth is the reliability test which ensures that the AC performs both the heating and cooling operation with ease and efficiency.
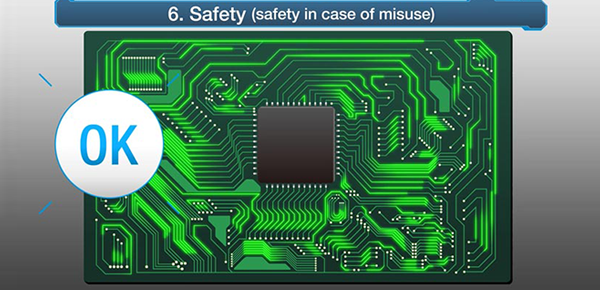
The sixth is the Safety test which confirms the PCB is not a fire hazard. Additionally, we also conduct safety test for each PCB to eliminate any chance of doubts.
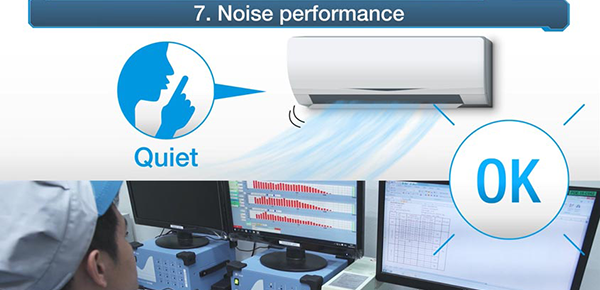
The seventh test in the Noise Performance test which makes sure that the indoor flap performs with ease without making any disturbing noise.
Furthermore, we conduct Abnormality test which enhances the product’s durability and safety during harsh weather conditions or rare conditions. Although, the design of the AC is flawless which ensures that no outdoor component can damage the product. However, we, at Daikin, test the products with artificial simulation to ensure zero problems. Every Daikin product produced in the Daikin production base goes through similar quality test criteria. Since we have the highest quality test criteria as compared to those laid by the air conditioning industry, these quality tests ensure that every product meets the highest standard of each country’s requirement.
Daikin’s passion for quality continues throughout their production with advanced production technology, where each component is carefully tested and assembled to create the final product. The superior precision with state-of-the-art technology and dedicated production teams guarantee that the technology of the AC remains highly durable and works immaculately, so that it consumes less energy.
Our aspiration to be the world’s leading expert has created a skilled and passionate team of professionals who are the reason behind the excellent quality air conditioners. Our specialized ‘Doju’ training centre at each production base makes it mandatory for every skilled production team member to attend the training sessions and enhance their skills. Strict performance evaluation is accomplished by trainers to ensure a consistently high level of work by the production team. We also organize a Global Skill Olympics which provides a platform for master brazers to share and enhance their skills, identify new techniques, and develop new ideas for our brazing expertise. To reduce re-work for identifying defect products, our IT system prevents human errors for occurring, even before quality inspection. In this system, every single part is uniquely barcoded and monitored throughout the entire assembly process in the HATA System. More automation means higher productivity, therefore, we have developed our own Automatic Guided Vehicle (AGV) which transfers required components from one lane to another, based on the information provided on the HATA system. The AGVs ensures that the right parts reach the right place at the right time. Similarly, in the factory, IT systems are used in harmony with the human to maximize production efficiency.
One of the main components in an AC is a refrigerant. It cools the interior. But if for any reason, the refrigerant leaks, it increases power consumption and reduces the air conditioner efficiency. Furthermore, refrigerant leakage is extremely difficult to detect and repair. To ensure zero defects in the refrigerant technology and guarantee utmost comfort, we conduct more than 8 refrigerant leakage tests to prevent fast, slow and very slow leakage. In addition, a zero leak committee is established to examine, record and analyze any leakage and report recommended measures to the committee. The improvements suggested are immediately put into action and diligently applied by the production team. To deliver the best quality products, we ensure 100% running tests commitment.
Our passion for quality, complete in-house development, quality testing, propriety training measures, personnel training, and commitment to safety continues to deliver high-quality air conditioners to people around the world made with passion and determination.